In this technique, the mold is not destroyed with each injection. It is permanent. It is made of steel for hot work. There are several Zinc Die Casting processes. Low-pressure casting currently represents around 20% of production, and its use is for parts with demanding mechanical characteristics.
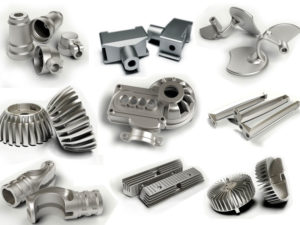
In this process, the liquid metal is injected at high speed and pressure into a metal mold.
The equipment consists of two vertical plates in which the mold holders that hold the die halves are located. One fixed plate and the other has moved to remove the part from the mold. A metered quantity of metal is poured into the container. Then it is introduced into the mold cavity using a hydraulically actuated piston. Once the metal has solidified, the mold opens, and the injected part is removed.
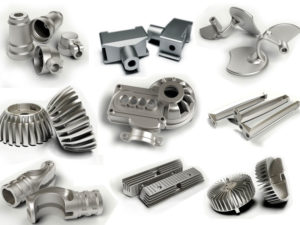
High-pressure casting
Die casting is a widely used manufacturing method for producing aluminium and other alloy parts by high-pressure injection of molten metal into reusable steel molds. Components made with die-casting technologies can achieve complex geometries, smooth or textured surfaces, making them suitable for a wide range of products and applications.
Advantages of die casting
Outstanding properties: High durability and a heat resistance of die casting products.
High capacity production: Allows the manufacture of large quantities of identical castings without the need for additional machining processes.
Profitability: The long useful life of the tooling results in the production of components with competitive prices in the market.
Complex geometries: Die-casting products are stronger and lighter than other comparable products made with different casting methods.
Components made by the die-casting result in a single part, which has no separate welded, giving more strength and stability to the manufactured components.
Advantages of Aluminum Die Casting
Aluminium die casting parts can be powder coated, anodized, painted with corrosion-resistant
lightweight aluminium die casting products are offered at competitive prices
Good mechanical properties ensure Die Casting precision is high and stability and flatness is good, even thin walls and complex shapes
Quickly dissipate heat, High thermal and electrical conductivity
Aluminium die casting products
A lights die casting product is produced by filling a molten aluminium into a metal mold cavity under high pressure. Dimensional precision and stability - Die casting produces Metal Machining Parts that are durable and dimensionally stable while maintaining close tolerances. The applications of ADC12 Aluminum are suitable for Auto, Led, Led, Telecom, Robert, Furniture, etc.
Die casting technology
The companies manufacture pressure casting parts that weigh between 5 grams and 12 kilograms. They use cold chamber die casting machines to cast aluminium, aluminium alloy, magnesium and other alloy products for our customers. For Zinc alloy components, they use hot chamber die casting machines, due to the melting point of Zinc based alloys of around 900 ° C. This would affect the tools, decreasing their service life due to large temperature gradients if cold chamber die casting machines are used.
The die-casting technologies and services have many advantages, such as high production capacity, high precision, high resistance and surface finishes, among others. Furthermore, they are aware of the initial investment associated with tool costs.
No comments:
Post a Comment